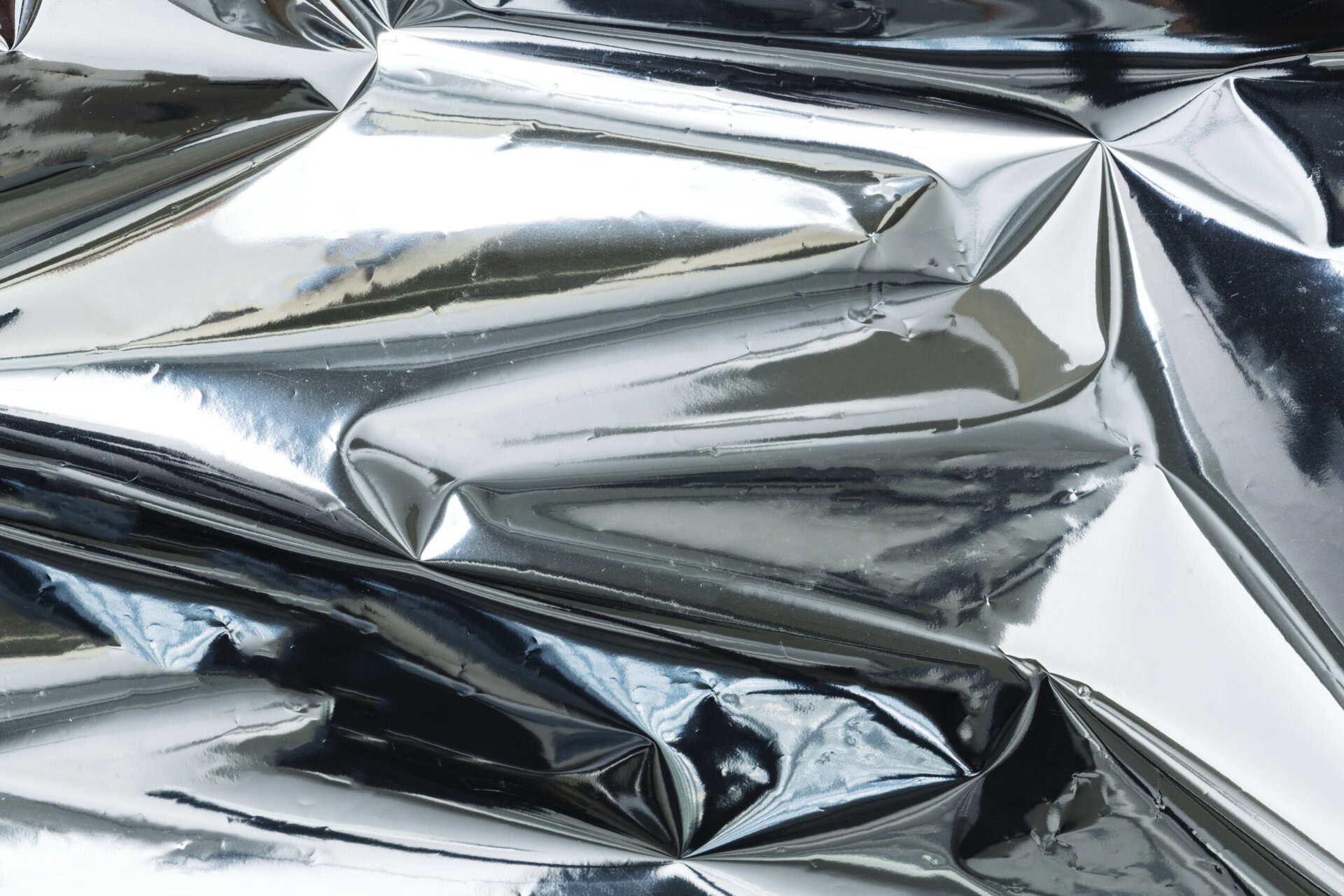
11 Jul How to Prevent Metal Fatigue in Custom Work Truck Components
When you rely on your work truck to perform under pressure, every component matters. From toolboxes to bumpers to support structures, durability isn’t just a feature — it’s a requirement. Understanding how to prevent metal fatigue is one of the best ways to protect your investment and keep your operations moving forward.
What is metal fatigue?
Metal fatigue is the silent enemy of high-performing equipment. It happens when a material is subjected to repeated cycles of stress and strain, eventually causing microscopic cracks to form and grow. These cracks weaken the structural integrity of the metal over time, often leading to failure without any warning. For custom truck components that deal with constant vibration, weight, and movement, fatigue can be a costly problem if left unchecked.
What causes metal fatigue in work trucks?
Your truck works as hard as you do, and that constant strain takes a toll. Common causes of metal fatigue include frequent loading and unloading, exposure to harsh environments, and long-term vibration. Temperature extremes and poor load distribution can also contribute. Even the finest metals will eventually wear down if they’re not protected against these conditions. That’s why it’s crucial to address the root causes before fatigue sets in.
How can metal fatigue be prevented?
Preventing fatigue starts at the design level and continues through maintenance. It begins with smart engineering that distributes stress evenly across components. Rounded corners instead of sharp edges, uniform thickness in metal parts, and properly placed welds all help reduce weak spots. Choosing the right alloy for the job is essential. High-strength, fatigue-resistant metals perform better under load and extend the lifespan of your truck’s components.
Regular inspection is also key. Look for signs of wear like discoloration, warping, or cracking. Early detection allows for timely repairs or reinforcements before the damage spreads. Proper maintenance schedules and attentive care are part of a successful fatigue-prevention strategy.
What are the methods for improving fatigue resistance in metals?
There are several proven methods that boost a metal’s resistance to fatigue. Surface treatments such as shot peening introduce beneficial compressive stress, which helps the material resist cracking. Carburizing or nitriding hardens the outer layer of steel components, creating a tough exterior that holds up to stress without giving in.
Welding techniques also play a major role. Clean, high-quality welds minimize the chances of fatigue starting at the joint. In some cases, post-weld heat treatment can relieve residual stress and improve durability. Coatings that protect against corrosion can also indirectly enhance fatigue resistance by preserving the material’s strength over time.
Companies like RC Industries combine these techniques when crafting custom toolboxes and heavy-duty metal parts for work trucks. That’s why their products are trusted by professionals who can’t afford failure in the field.
Make the Smart Investment
Preventing metal fatigue isn’t a luxury. It’s necessary for anyone who expects top performance and long-term value from their truck components. By investing in smart design, quality materials, and proper maintenance, you can avoid costly downtime and keep your equipment running strong. If you’re looking for custom metal components built to last, RC Industries delivers American-made durability backed by engineering that puts fatigue in its place.
Need a custom metal fabricator?
Looking for professional help? Transform your operations with RC Industries’ durable, custom toolboxes and precision metal fabrication! Get started today at RC Industries and experience quality you can trust. Contact us now for your free quote!